Finally, we have a fence! Now the golfers can no longer come into our yard – and pool. Someone actually had the gall to climb into the pool when just the rebar was in to retrieve a golf ball.
The gunite was applied today. I have seen this on TV, but never in person. It takes a lot of strength to hold onto the hose. The weather was perfect (for this application) to allow the concrete to dry slowly; cloudy and cool. It was one of the coolest days we have had – high 60s and breezy. I was freezing :).
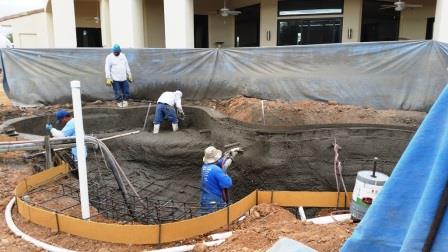
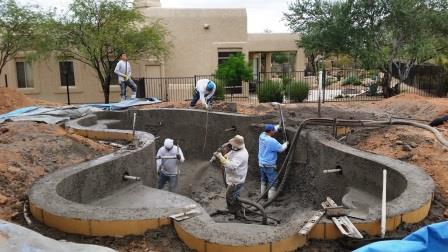
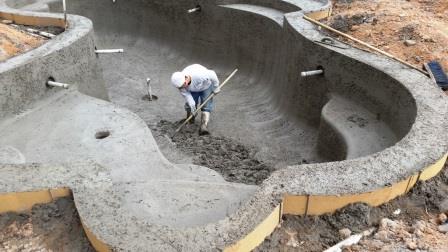
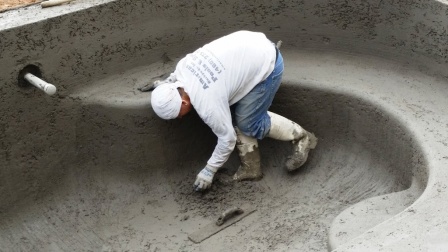
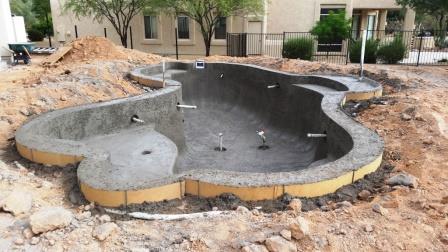
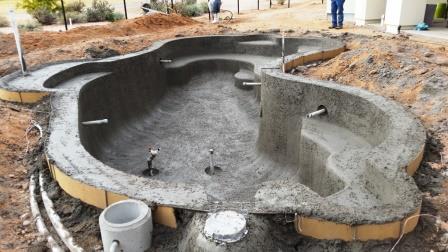
The pool fence posts were set today. The fence rails cannot be attached until the pool is completed so they have unlimited access.
We passed our first pool inspection of the plumbing, electrical work and the rebar on Tuesday, Nov 25. Construction of the pool will resume after Thanksgiving.
After a call to the County Supervisor’s office on Tuesday, we received a call from the County’s Ombudsman. She was able to get the reviewer to release his comments the same day. The reviewer brought up 3 items that were already notated on the plan (but he didn’t see them) and one short fence section that needed to be heightened. The engineer revised the fence notations and our builder and pool contractor took copies to the county this morning. Thanks to the Ombudsman, they were able to get the permit approved while on site. The expedited review process is suppose to take 3 days – it took 4 weeks! The builder called for the first of 6 inspections on the pool and it was scheduled for Tuesday. The fence will need 2 additional inspections.
All the electric and lights were installed today. Now we sit and wait on the county again! The permit was submitted on 10/24 as an expedited review (3 days) and we still do not have any action on it yet.
I missed the excavation for the pool while I was in Colorado visiting friends and family. The dimensions for the pool were marked off on 10/29 and the hole was dug on 10/30.
The plumber brought and installed the new water heater today. Right away we could tell the difference in the sound. Hopefully, this third one is a charm. The “Mirror Man” installed all the bathroom mirrors. We are getting down to the last leg on the inside of the house.
The oven repair man finally returned today (Wednesday). I now have a working oven and microwave. The builder still has to attach the water line for the steam option. I had read several reviews about other brand ovens burning out the control panel when the self-cleaning option was used. I also have a neighbor whose oven control board burned out when she used the self-cleaning for the second time. I asked the repairman about it and he told me to never use the self-clean option. He said they are not made to perform the job without harming the control boards.
The cabinetmaker finished installing all the cabinet faces except two. He still has to finish one desk face and the cabinet and door for my appliance garage.
The painters returned today and painted the foundation under the stucco, the front door, and touched up all the interior walls.
The cabinetmaker came today to install the cabinet faces. He had told the builder that I could place things in the cabinets. However, he did not clarify that I should not place anything in the drawers – almost all my bottom cabinets are drawers. To apply the faces, he had to empty all the drawers (all over the counters and island) so he could remove them and stand them up on the faces to attach them. I spent the evening repacking everything back in the drawers – 1 step forward; 2 steps back. The bank of pot drawers were the wrong size, so I still can’t put my cooking utensils and pots away. At least the non-working oven and microwave make good storage spots. In addition, the knobs we bought did not come with screws long enough to go through the drawer face and box. The builder had to go buy screws and will return tomorrow to install the knobs so I can open the drawers. But, I must say, the cabinetmaker did a great job. The cabinets are beautiful.
Speaking of the oven, I had an hour long fight with KitchenAid’s customer service department yesterday. I told a supervisor that a month was unacceptable to have a brand new oven repaired. He could not have cared less. The only thing he did was look to see when the parts would be in. He refused to do anything else. Guess who won’t be purchasing any KitchenAid appliances again.
The second hybrid hot water heater is also on the blink (we must have done something to make the appliance gods mad). The electric option works, but the heat pump option is not heating the water. However, the manufacturer, Rheem, actually understands customer service. They are going to have their plumber go to Home Depot to pick up a new one and come out to install it so the builder does not have to deal with it again.
We had our re-inspection today (10/15) and passed – yea; now we are legal. The window well grate was slightly too big since the stucco corners were not quite square and took the builder and my hubby a long time to make it fit.
We had our final inspection Wednesday (10/8) and failed. The ladder has been installed in the escape well from the basement bedroom, but the grate wasn’t on the top yet. We also needed clips on a few breakers that share a neutral (not sure why because the neutral doesn’t carry any power), a spring hinge on the door to the garage and the smoke detectors outside the bedrooms must be dual carbon monoxide/smoke detectors. The inspector for our area was on vacation so the boss came out. He said to the builder “you know they aren’t supposed to be living here before final inspection, but I didn’t see anything.”
The electrician came today (Friday) and swapped out the smoke detectors and installed clips on the breakers. The window well grate should be here on Monday or Tuesday and the builder will put the hinge on the door right before inspection so it makes it easier for us to carry things in and out. He should be able to schedule a re-inspection for Wednesday.
The service tech for the oven/microwave was scheduled to come out yesterday and didn’t show up. The rep at the service company said they had no record of the appointment (after waiting 11 days for them) and would send a tech out Friday and then called back this morning and said the tech was too busy today and would be here Saturday morning. Needless to say, my hubby and the builder were livid. The builder called his sales rep, who called the owner of the company, who called the service tech directly and the service tech was there within 2 hours. Unfortunately, the unit needs a new control panel, which must be ordered. We may have a working oven by Thanksgiving! I actually miss the microwave more than the oven. I have relearned how to cook and reheat everything on the stove, which is induction and is wonderful. I will never go back to an electric or gas stove.
The driveway,sidewalks and the front porch pavers were completed today. It is nice to not have to stomp though the dirt to get into the house. We still can’t fit our cars into the garage due to the supplies and empty boxes. The front door still has not been stained – we really aren’t going to leave it pink.
The tiler completed installing the backsplash in the powder room and basement bathroom and grouting the tile he installed on Sunday. Now the tile is finished. The plumber came back today and installed the toilet in the powder room, steam hookup for the oven, the dishwasher and ice maker. As most of you know, we drink a lot of ice water and the refrigerator can never make enough ice for us, so we decided to install an ice maker. Well, it makes a lot of ice, but it is very noisy! I’m not sure it is going to survive so we haven’t peeled the plastic film off yet.
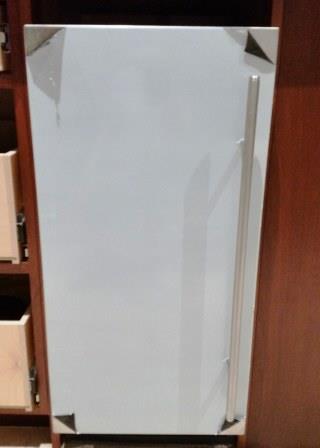
The tiler worked 7 days again this week. He installed the backsplash in the kitchen, master bath and the guest bath on Sunday. The backsplash in the kitchen contains a few light switches, but it does not contain any outlets. All the outlets are under the upper cabinets – all 19 of them! They are in strips mounted on the bottom of the upper cabinets. Some have 2 outlets and 2 are long ones with 5 or 6 outlets. Plus, there are 2 at each end of the island. I jokingly told the electrician that I didn’t think I had enough outlets in the kitchen. Then I asked why I would ever need that many. He said “When you throw a big party, there will be plenty of space to line up and plug in crock pots, warming dishes, coffee pots, blenders, etc.” He does have a point.
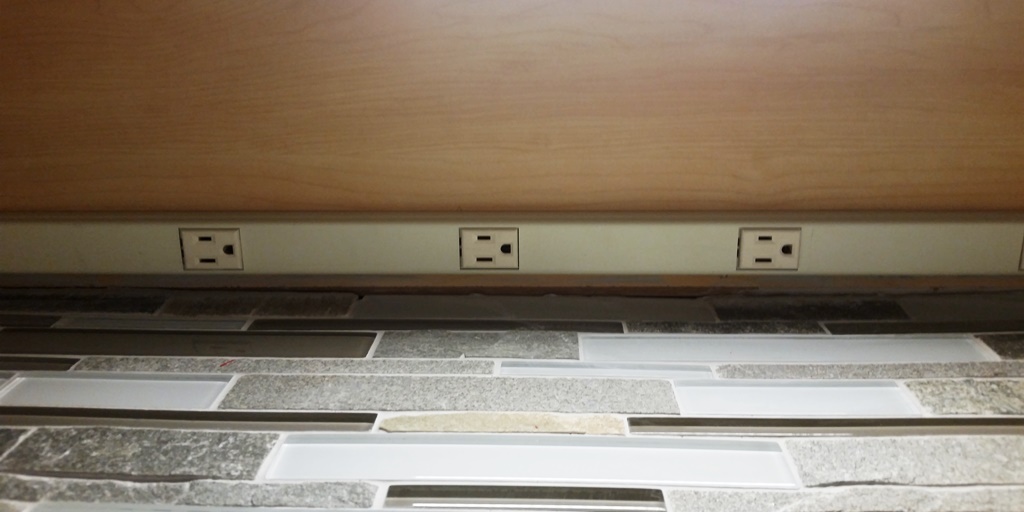
Some days it is the small things that make me happy, like this cute little button door stop. I have never seen these before, but they are much nicer than the larger door stops.
Other days, it is the large things, like having the floor tile finished. All the kitchen, hall, foyer and family room tile was grouted today except for a small section in the kitchen.
I was apprehensive about using glossy tile, but it turned out beautifully. We used this same tile in our master bath, hallway to the family room, foyer, family room and dining room. It has tan, cream, gray and some blue shades in it. The kitchen, laundry room and hall to the garage tiles are a matte finish.
The sand and pavers for the driveway and the front entrance were delivered today. They will be installed on Monday. We have been parking in the cul-de-sac and have our golf cart stored in a friend’s garage. Due to all the tile, supplies, the rest of the appliances and boxes in the garage, nothing else would have fit anyway.
The trim carpenter installed the handrail on the basement stairs yesterday and patched the walls. The carpet contractor came back today to carpet the stairs. We didn’t want the carpet installed until after we moved so it would stay clean.
The tile was installed under the refrigerator today. It’s a good thing we had an outlet nearby. We will be able to slide it back into its cabinet tomorrow. The laundry room was grouted so we were able to bring in and hook up our washer and dryer. However, one of the movers must have stepped on the washer drain hose and split it. We ended up with water all over the floor – another trip to Home Depot – sigh.
All the furniture and boxes were in the family room since the dining room and kitchen did not have any tile. Now that the dining room is tiled and grouted, we had to move all the furniture into the dining room. It’s a good thing we sold our family room furniture to the people who bought our old house and have not had our new sectional delivered yet. As they tile and grout, we continue to move boxes between rooms everyday.
Since the tile was installed on the sink and cook top side of the island and we could not walk on it, we had to go out for dinner – what a shame! The oven and microwave are not working. The dealer is so busy that we have to wait until next week for a service call.
Since we do not have any faucets in the kitchen yet, we had to use the bathroom to wash dishes. The plumber is scheduled to return tomorrow. We have a cook top and the refrigerator, but no oven, microwave or dishwasher. The basement is completed, except for the cabinet faces and the flooring is installed in the bedrooms, bathrooms and den. We have tile in the family room and although it is not grouted, we were able to place the kitchen, family room and dining room furniture and boxes on the tile.
Moving Day(s)– 9/25 & 9/26!
Even though the house is not completed, since we had to be out of our rental and didn’t want to move twice, we moved in. Somehow in the chaos I forgot to take pictures! It wasn’t easy moving into an unfinished house (and I feel sorry for the contractor having us underfoot), but it is nice to be in our own home and out of the rental house. Thanks to our family and friends that came to help. We could not have done it without you.
The carpet was installed in the basement and the bar was completed.
The granite and faucets were also installed today in the guest bath.
The painters were back to finish the basement closets and bathroom so the tiler had to move upstairs and start on the floors.
Refrigerator cabinet. The paint looks blue in this picture, but it is grey with a blue undertone.
The person installing the tile worked Saturday and Sunday and completed the guest bathroom shower. He will move on to the basement bath shower this week. Due to the rain and flooding, he did not work today.
We repainted the master bathroom Friday afternoon and Saturday morning before they installed the cabinets. We’re not real happy about this color, but it will do for now. We left the bedroom blue along with the toilet room and the walls that surround the bathtub. We decided to live with them awhile and then decide if we want to change them.
The builder and his trim carpenters started installing the cabinet boxes today.
I can’t wait until they have finished applying the final coat on the stucco. It makes a mess and I’m getting tired of looking at the scaffolding. The color is a tan with a slightly yellow base, but looks different colors depending on the angle of the sun.
The painters have been working on priming and painting the ceilings. By the end of the day, they are covered head to toe in paint. It’s been so dry this week that the spray that falls to the floor dries before it gets there. The floor is covered in a fine powder from the paint.
The woodwork is covered with paper and the exterior doors and windows are covered with plastic. I don’t know how the painters breath. I am not able to stay in a closed room with the stain or paint for more that two minutes. The tiler won’t be able to work in the house today or tomorrow due to the smell.
The master and the one of the guest showers are “snail” showers, which are popular here. They do not have doors. You walk in and turn 180 degrees into the shower. We have one in our rental and I thought it would be drafty, but it’s really not. They save on having to keep any glass clean.
Our tiler is very meticulous. His cuts are perfect. The cutouts for the lights are almost perfectly round. He has completed applying the tile in the the master shower and is working on the guest showers. He will grout them all later.
The painters removed all the doors so they could stain and lacquer the tops and bottoms to keep any moisture out of the wood. Also, removing them negates the need to cover them with paper while they paint the walls and ceiling.
Building the closets. This is part of the master bedroom closet. The shelves on the right make up my shoe rack. Ok, maybe my hubby can have a shelf or two for his shoes.
The painters stained the doors and woodwork today. The stain was sprayed on and then hand sanded. It was finished with a lacquer sprayed on top.
The interior doors and woodwork are knotty alder, which is very popular here for doors and cabinets. Our cabinets will be select alder (no knots!).
Our builder said his worst nightmare is a leaky shower; they are extremely expensive to repair. The drywall contractor placed the cement backer board in the shower. Our builder had his tile installer paint the cement board on the walls with a liquid red waterproof membrane. Next, he applied a layer of brown waterproof membrane and then placed another layer of cement board on top which will also be painted with the red waterproof membrane. All that should make them nice and dry :).
They are applying the texture to the drywall. We choose the lightest texture – Santa Fe. It is a very subtle low profile drywall texture. It can be described to appear as two smooth layers of drywall, the top layer allowing the lower layer to show through in random areas.
The drywall installation is complete. The next step will be to place another coat of compound on it to create a slightly uneven surface. They do not smooth out the compound here; the walls are textured. They range from a very light texture called “Santa Fe’ to a very heavy texture.
The electric company came again today to inspect the main line and failed it again because the stucco guys covered the main box with a small piece of plastic so they didn’t get stucco on the box. The electric company employee was unable to use his common sense to pull it off to look in the box – and people complain about government workers! They should be out tomorrow again for the inspection.
The first coat of stucco is completed except for a small section beside the front doors and a small section on the back patio. The window company sent the wrong size window for the kitchen and we decided to keep it rather than wait on a replacement. The contractor needs to reframe the window opening before they can complete the stucco around the window. I thought the drywall people made a mess, but the stucco guys trump them.
In order to apply the stucco on the roof line and the chimneys, they had to load it into buckets and pull them onto the roof with a rope.
These guys are at our house until 7:00 at night. They work 12 hour days Mon-Fri and shorter days on Saturday. Sanding drywall is not my idea of a fun job.
I haven’t posted any pictures this week due to a camping trip to the Coconino National Forest outside Flagstaff. I will try to post some pictures of the trip on the “Local Interests” and “Critters” pages this weekend.
They completed installing the drywall on Tuesday; what a difference it makes! They have been working on installing the corner trim, tape and mud. The HOA approved the pool design. We are still waiting on the permit from the county. We still don’t have electrical service. The county did not pass the main hookup due to a couple bolts missing where the main connects to the box.
The drywall installers came today. They worked in three teams of two, one cutting and one hanging, in different areas of the house. They were able to get the garage, the back patio ceiling, and the ceiling and upper walls in 3/4 of the main floor completed.
Boy, am I glad I don’t have to clean up after this crew – they make a mess!
They finally dug the trench to install the main electrical line. It will be nice once the electric company connects it to the house so we won’t have to use the generator when Tom works in the house. Yes, if you know him, you know he can’t stay away. He selected certain items to install himself: speaker system, security cameras, TV and Internet cables, and the niches in the TV wall. He had me crawling in the rafters helping him to string wires across the house one weekend and I helped to seal all the small spaces between the framing to keep the heat and small critters out. He has also helped our contractor with many small items. It will also be nice to be able to use the shop vac to clean up, when we have to, instead of a broom.
The drywall was delivered and stacked in every room in the house. They were not able to get the large sheets down the stairs so they had to remove the window in the basement window well so they could drop the drywall through the window opening.
The roof tiles were delivered and stacked on the roof so the weight will help to settle the house.
We met with the pool contractor and the cabinetmaker today. After we select a pool design, we must submit the plans to the county for a pool permit. I hope it is not as painful as it was in January waiting on approval for the footer changes.
The Icynene foam insulation installation was completed. It was fun to watch (from a safe distance) the sprayed on liquid fill every nook and cranny.
The stucco guys worked on the trim around the top of the house today. They should finish tomorrow.
We were not allowed in the house today because they were installing the spray foam insulation. The installers wear air purifying respirators during the process.
Paper measurement tools are placed on the trusses and walls to ensure the proper depth is achieved. The insulation on the ceiling will be 8 inches thick, the walls 5 inches (although they filled the 6″ wall studs and the ceiling in the picture below looks like it’s 10″) and the basement and garage will be 3 inches. The white foam looks like snow on the ceiling :).
They are still working on placing the foam and lath on the house for the stucco. They work at the same snail’s pace as the air conditioner sub-contractor.
The roofer completed installing the battens on the roof on Saturday. Next, the concrete tiles will be stacked on the roof so the weight will help to settle the house. The drywall isn’t installed until the tiles are stacked on the roof.
We are placing a radiant barrier and scalloped battens on top of the felt paper on the roof. The radiant barrier will reflect the heat from the roof. The scalloped battens will allow the heat to flow from the edge of the roof up and out the ridge vents.
The roofer started installing the felt paper today. The stucco sub-contractor is almost finished with installing the paper, foam and lath on the exterior of the house.
The air conditioning, electric, plumbing, gas and fire sprinklers have all been roughed in. The plumbing and gas were inspected on Monday and passed. The electrical and fire sprinkler systems will be inspected tomorrow. The orange pipe in this picture is the fire sprinkler system (required by code).
We were hoping to get the felt paper on the roof before we had any rain, but we missed it by one day. We had about an inch of rain with 1/2 inch inside the house. We swept the rain off the wood sub-floor and luckily it dried without any issues. The roofer was suppose to be here two weeks ago, but due to their schedule, they were not able to commence work on our house. The felt paper was delivered today and the roofers will be here tomorrow.
They placed the first coat of the elastomeric roof coating on our roof walk deck this week.
There was a host of activity today. The framer had to come back to run a soffit in the basement for an air conditioning duct. The air conditioning contractor should have all the duct work completed today. The plumber is almost finished with the plumbing rough-in. The roof contractor installed the coating on the walk deck. The stucco crew was there yesterday to begin placing the paper and foam board on the exterior.
The framers finished on Friday and we passed the frame and shear inspection on Monday. All the windows and doors that were delivered have been installed. Some of the windows were cracked on arrival and others were not included in the initial shipment. The plumber worked on roughing-in the plumbing on Tuesday and Wednesday and will be back next week. The air conditioner contractor started on the duct work today.
This ceiling dropdown will be over the kitchen island. We decided not to include the soffit as we thought it may make the room too busy and detract from the dropdown.
The framing is almost completed. They have to finish the soffits, the other ceiling designs, the bar and some odds and ends.
This frame will be placed on our bedroom ceiling.
The frames on the floor will become the family room ceiling soffit.
This is one view from the walk deck on top of the rear patio roof.
This was by far the most difficult task, excluding the roof, in the framing process.
They worked on completing the inside doorway arches and starting placing the roof trusses on the back patio today.
This is the frame for the front entryway roof and columns. It will be interesting to see how they lift it upright into place on top of the column footers.
They brought in a crane today to put the glulam headers in place to hold the roof trusses.
Now that all the underground and prep work has been completed, we are seeing some real progress. This is where it gets exciting.
Our builder captured this picture of a diamondback rattlesnake on the lot while waiting for the pre-slab inspection.
The stem wall frames were completed and passed the county inspection today.